For medium / large pipe or profile manufacturers, traditional artificial mixing, conveying and feeding can not meet the needs of the current automatic production. Therefore, a complete set of automatic control system from stocking of raw materials, mixing material to centralized transportation, is essential.The complete set of automatic chemical plant customized for customers by Liansu Machinery includes the storage of raw materials, the delivery of materials, weighing and mixing, and the automatic delivery of the mixture to the production of the extruder.
Liansu Machinery is committed to building a central control automatic mixing and feeding system to reduce labor costs, improve product quality, improve production management efficiency, and provide a better working environment.
Case One
Case One
A customer’s workshop built early, the mixing room and extrusion production line is in two different places, the production line needs workers to carry material through a car from the mixing room to the production line material area. The distance between two places is about 150m.
After the transformation, the workshop reduced 5 employees, if the monthly salary is RMB5000, the cost we save of one year is RMB300000, the workshop environment is better after transformation, the staff stability is higher.

Workshop Feeding Scheme
At present, there are totally 16 production lines, 9 mixing machines and 1 formulations in the workshop. After comprehensive consideration, we decide that every 2 mixing machines transport through dense phase and sent to the intermediate silo on the production line, and each intermediate silo corresponds to 1 pipe chain, 4 extrusion lines, and the rest of the mixing machine is spare, the mixture can be sent to each machine.
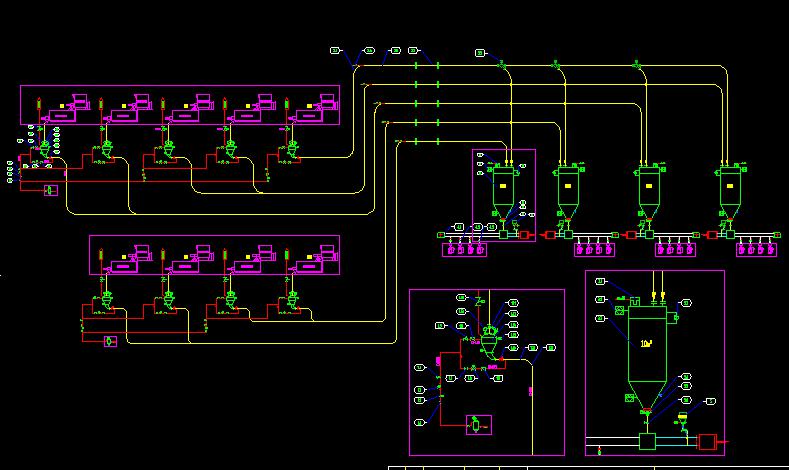
Before The Workshop Transformation
Mixing machine feeding,artificially back and forth convey the material to machine,this mode is time-consuming and laborious,the working environment is too bad to satisfy the modern environmental protection production standard.
After The Workshop Transformation
Material conveying pipeline outside the workshop.
The production line feeding area is now automatically supplied to each production line through the chain conveyor, without manual feeding.After transformation, dust-free transportation is achieved, which meets the needs of production and provides a healthy production environment.
Case Two
Case Two
The PVC workshop of B customer has been built from the original design according to the fourth generation plant.The middle part of the workshop is the material mixing area, totally 4 layers, the fourth layer as raw material storage area, the third layer as raw material weighing area, the second layer as the mixing machine, and the first layer as the extrusion line production area.The raw material feeding area is in another workshop on the first floor, and the material is transported to the raw material storage area of the fourth floor by pneumatic conveying.
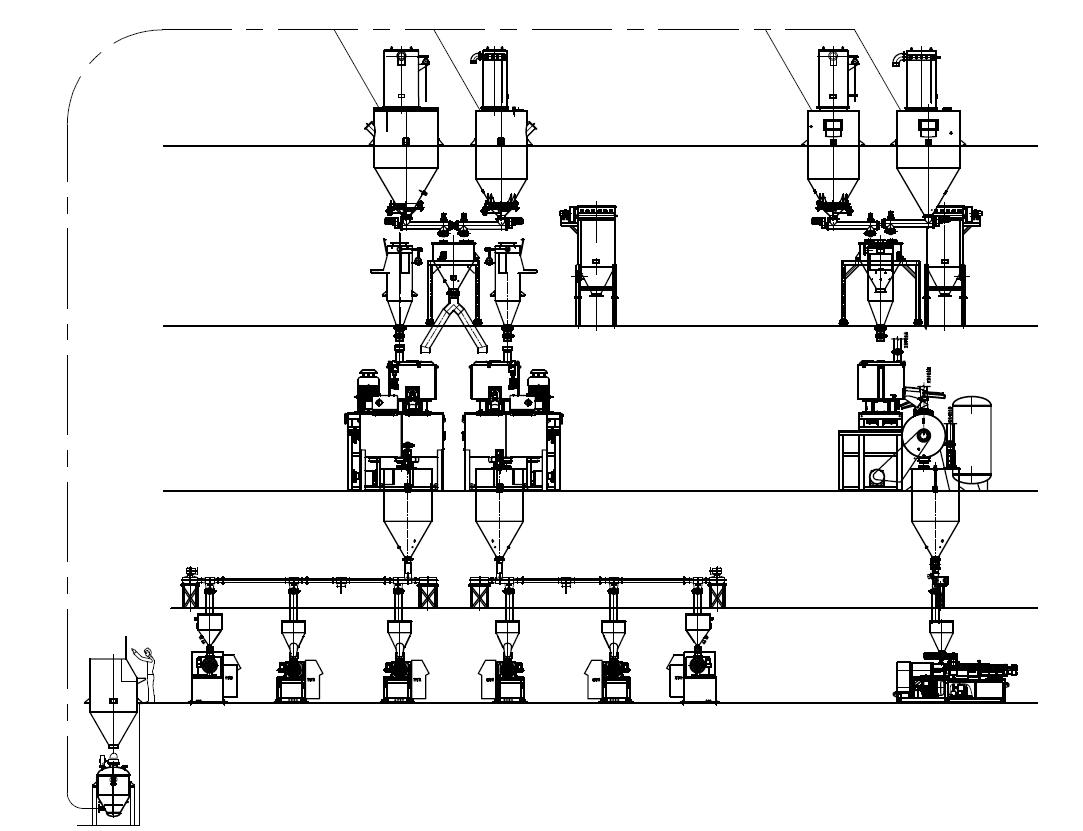
Workshop Feeding Scheme
Centralized feeding area is conducive to efficient management of raw materials.
Above the feeding station, a ton bag feeding hole can be set up, the single and double station can be selected for the feeding station. For double-station feeding station, two people feed at the same time to reduce the labor intensity when the production task is heavy.
The storage silo is used for the storage of the main material PVC and CaCO3, and the pressure release valve is installed above the silo. When the pressure of the silo reaches the set value, the valve automatically releases the pressure and plays the role of safety protection.

Each kind of material passes through the storage hopper, and the below is the screw type feeder. The screw feeder is controlled by the computer. The material is conveyed to the electronic scale, to weight each kind of material in turn.
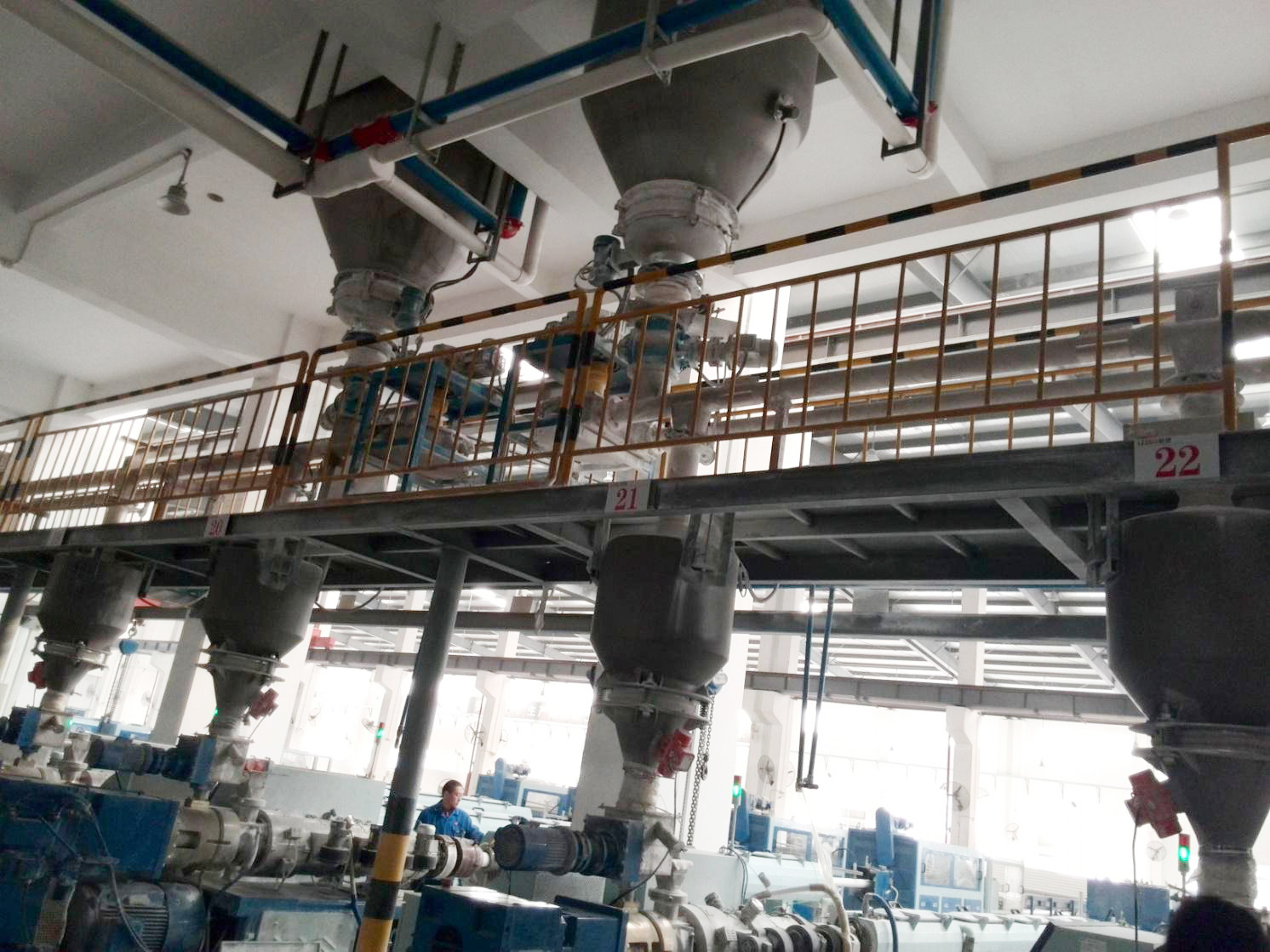
Through the chain conveyor, each material is automatically delivered to the extrusion production line, and the manual labor operation in the intermediate process is omitted.
Case Three
Case Three
C customer's PVC workshop automatic feeding PVC and CaCO3, through manual feeding, low pressure continuous delivery, stored in five 100m3 large silos, and the material is delivered to the mixing machine through negative pressure weighing,then the mixture is conveyed to machine for using through the silo pump.The system uses a large silo to store the raw materials, and the material in the silo can meet the 8 hours' use of the machine. In this way, the material can be fed on the night shift and the lowest electricity cost for daytime use.
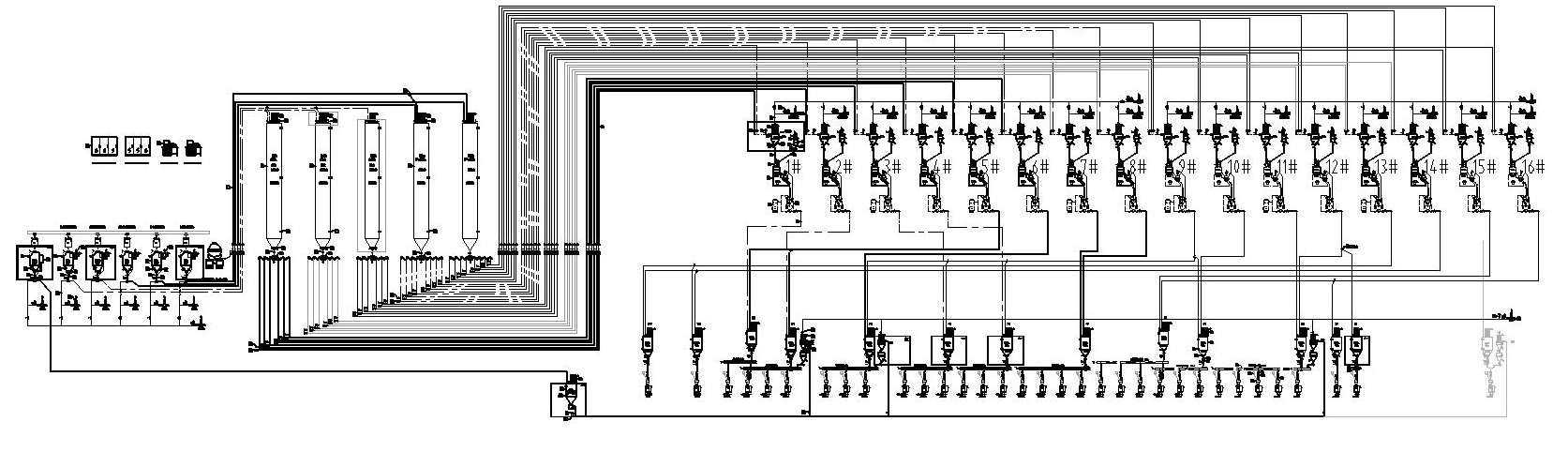
Workshop Feeding Scheme
Manual feeding workshop
Material conveying in low pressure
Outdoor 100m3 PVC and CaCO3 storage silo, the bottom of it is the distribution box of negative pressure suction.
Main material weighing and formulation feeding workshop
Mixing workshop,uses silo pump to convey the mixture